Arc Stud Welding is generally used to weld large diameter fasteners to rougher and thicker base metals. Arc studs must have one end of the fastener designed for Arc welding. Mild steel, stainless steel, and aluminum are applicable materials for Arc stud welding.
Arc stud welding requires a dc power supply to create the arc, a stud welding gun, metal fasteners, and in some cases ferrules. There are three common techniques of Arc stud welding: Drawn Arc stud welding, Short Arc stud welding, and Gas Arc stud welding.
Drawn Arc Stud Welding
In the Drawn Arc technique, the stud is loaded into the stud gun chuck, and a ferrule (a disposable ceramic shield that contains the molten pool of metal) is placed over the end. The gun is placed against the work position. When the trigger is pressed, the dc power supply sends a signal that energizes the gun’s internal lift mechanism lifting the stud, drawing the pilot arc. The pilot arc establishes a path for the weld current which initiates after the pilot arc. Upon completion of the proper arcing time, which is proportional to the square area of the surface being melted, the lift mechanism is de-energized. This causes the stud to plunge into the molten pool of metal. A plunge dampener is often used on larger studs to decelerate the stud’s movement onto the molten pool, minimizing splash. As the stud and the base metal join, the metal begins to solidify and the weld is created. The gun is lifted, and the ferrule is discarded.
The Drawn Arc technique uses flux embedded in the stud to cleanse the atmosphere during the weld. During arcing, the flux is vaporized and combines with the contaminating elements in the atmosphere to keep the weld zone clean.
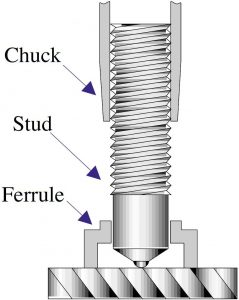
1. The weld gun is positioned with the ferrule and stud in place. The main gun spring is compressed.
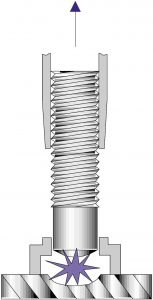
2. The trigger is pressed and the stud lifts off the workpiece. An arc is created by a dc power supply, melting the full diameter of the stud and the same area of the base material.
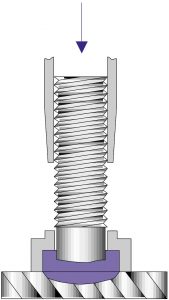
3. After the welding time is completed, the main spring plunges the stud into the molten pool of the base metal.
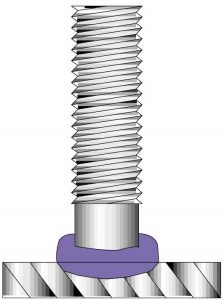
4. The gun is withdrawn from the welded stud. The ferrule is broken away and discarded.
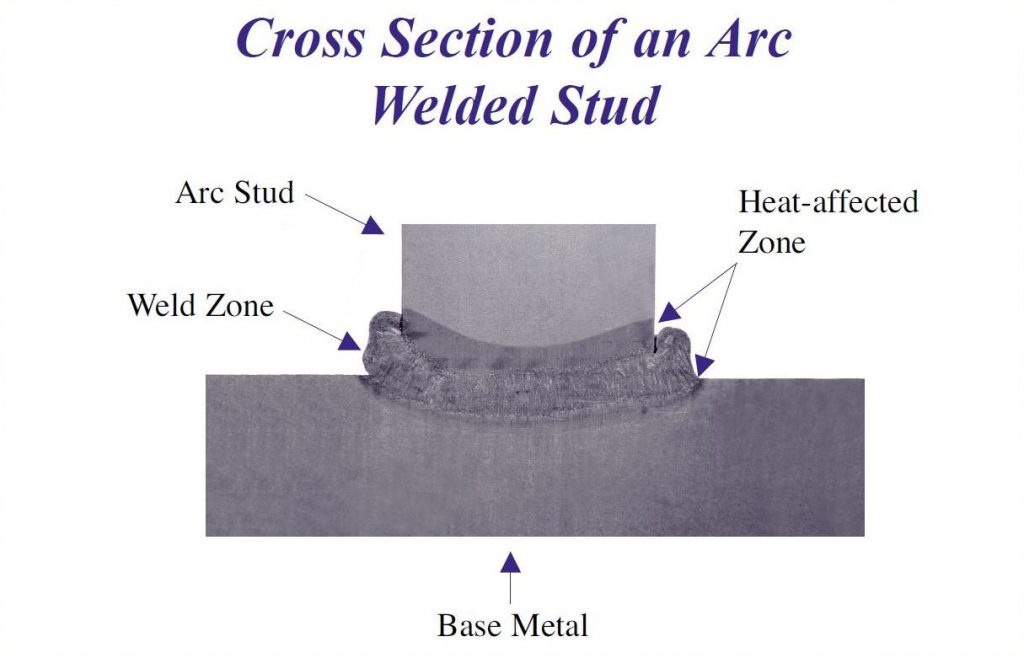
Short Arc Stud Welding
The Short Arc technique is much like Drawn Arc, yet it uses no flux load or ferrule, and it offers the shortest welding times of the Arc stud welding techniques. It is characterized by high currents and short weld times. While it may be suitable for many high volume applications, it can produce porous welds and should therefore be selected when speed and cost are a priority over weld strength. The short weld times minimize the effects of porosity while the high current maintains the needed energy.
Gas Arc Stud Welding
The Gas Arc technique uses inert shielding gas with no flux or ferrule, making it easier to automate, but it provides less fillet control and less depth of penetration in comparison with the Drawn Arc technique. In Gas Arc welding, a spark shield, which delivers gas, replaces the ferrule. The stud is loaded and the gun is positioned for welding. When the user pulls the trigger, shielding gas (“gas pre-flow”) floods the welding zone. The stud is lifted, and an arc is generated. While the stud remains lifted, the weld current melts the stud and base metal. When the arc time is complete, the gun is plunged into the molten pool. A post-flow of gas is introduced to the weld, flowing until the molten metal cools. The gun can then be removed. Since no ferrule is used, this process lends itself well to automation and robotics.